治具とは?設計から製作における最適な手順と基礎知識を解説
製造工程において効率的で再現性の高いプロセスを実現する為には最適な治具を設計、製作し、適切に使用することが欠かせません。
治具に求めれる機能は位置決め、整列、搬送、固定(クランプ/チャック)、移載、反転、ポカヨケなど多岐に渡りますが、単一の機能のみでなく、複数の機能を1つの治具に盛り込むことも珍しくありません。(例えば固定治具は位置決め機能を兼ねるのが一般的です。)
今回は「そもそも治具とは何か」「治具の種類や役割にはどんなものがあるか」「治具の設計から製作までの基本的な流れ」などを解説するとともに、当社が得意とする「エッチング加工を用いた治具の設計、製作」について紹介、提案していきたいと思います。
治具とは何か?基本から学ぶ治具の役割と種類
治具は英語の「JIG」の当て字で読み方は「じぐ」です。漢字だと「冶具」と書かれることもあります。
加工や組み立ての際、加工対象(ワーク)を固定したり、加工位置や部品取り付け位置を指示、誘導したりする為の器具の総称で、「治工具」や「補助工具」と呼ぶ場合もあります。
主な機能、役割として、
- 加工や測定時にワークを固定して姿勢を安定させる。
- 組み立てや接着時にワーク同士の位置を合わせる。
- 工具や部品などを所定の位置にガイドする。
- 塗装や溶接の際に加工部以外を保護(マスキング)する。
- 複数のワークをまとめて取り扱えるようにし、作業を効率化する。
などが挙げられます。
そして治具を用いることで、
- 品質の安定化
- 作業の効率化
- 訓練機関の短縮
- 人的ミスの削減
などの効果が期待できます。
代表的な治具の種類と特徴
固定治具(クランプ治具/チャッキング治具/バイス治具など)
ワークを所定の位置に固定し、安定した姿勢で加工、組み立てなどの作業を行う為の治具です。
ワークのサイズや形状、作業の種類により最適な固定方法を選定する必要があり、ワークの固定箇所、固定方法、固定力などのパラメータを最適化することで作業性や加工精度の向上に繋がります。
位置決め治具
同じ作業が繰り返し行えるようにワークや工具の位置を決める為の治具です。
突き当てのような簡易的な方式のものもありますが、多くは固定機能も兼ね備えます。
作業の再現性を向上させることで、品質の安定化に繋がります。
搬送治具(キャリア/トレイ/パレットなど)
複数のワークをまとめて搬送する為の治具です。
搬送自体ではなく、治具上のワークに所定の処理を加える為に工程間を搬送するのが目的であることから、必要に応じてワークを位置決めしたり固定したりという機能を持たせることもあります。
また、耐熱性や耐薬品性など使用される工程に適した材料を選定する必要もあります。
マスク治具(マスキング治具)
塗装や接着剤塗布、溶接などの工程で加工箇所以外を汚さないように保護する治具です。
テープ等を用いたマスキングではワーク毎に作業が必要となりますが、マスク治具を使用することで段取り時間を大幅に短縮することができます。
ペーストの印刷やパターン成膜に用いられる「メタルマスク」と呼ばれるものもありますが、これらもマスク治具の一種と見ることができます。
治具の材質選び
アルミ、ステンレス、鉄、銅、樹脂、セラミックス、カーボンなど、治具に用いられる材質は多岐に渡ります。
材質の選定に当たっては治具の用途、使用されるプロセスの環境、許容されるコスト等を複合的に勘案することが重要です。
例えば、
- 熱はどのくらい掛かるのか
- 耐薬品性は必要か
- 導電性、または絶縁性は必要か
- 許容される重量はどの程度か
- どの程度の強度が必要か
- 必要数量はどの程度か
- 必要な精度はどの程度か
などの観点から、それぞれの特性に応じて材料を選定していきます。
樹脂製の治具は軽量、安価で絶縁性に優れる反面、耐熱性、耐薬品性では劣ることが多いです。アルミは切削加工性が良く、金属の中では軽量ですが、強酸や強アルカリには侵されてしまいます。ステンレスは高強度で薬品や熱にも強いですが、重量面がネックになることがあります。
各材質のメリットとデメリットを正確に把握し、適切な材質を選択する必要があります。
治具製作の工法や特徴と比較解説
治具製作の代表的な工法
治具の製作には様々な工法が用いられます。
代表的な加工方法として切削加工、ワイヤーカット、レーザーカット、エッチング、3Dプリント、樹脂成型などがあります。
その他、曲げや接着、溶接、拡散接合、塗装、めっき、熱処理など複数の工法を組み合わせ、必要な機能を満たす治具を製作していきます。
当社ではエッチング加工で作成した金属部品を溶接や拡散接合で積層し、耐熱性や耐薬品性に優れた複雑、高精度な治具を多く製作しております。
各工法の比較
エッチング加工 | 切削加工 | レーザーカット | ワイヤーカット | 樹脂成型 | |
形状の自由度 | 〇 | 〇 | △ | △ | △ |
加工精度 | 〇 | ◎ | 〇 | ◎ | △ |
材質の自由度 | △ | ◎ | 〇 | 〇 | △ |
イニシャルコスト | 〇 | ◎ | ◎ | ◎ | △ |
少量時コスト | 〇 | ◎ | ◎ | 〇 | △ |
量産時コスト | 〇 | △ | △ | △ | ◎ |
治具設計の流れ
治具設計の基本ステップ
①治具を導入する目的や要求品質、使用環境、その他前提事項をできるだけ明確にします。
「何のために治具を使用するのか」「誰が使用するか」「耐熱性はどの程度必要か」「耐薬品性は必要か」「許容重量は」「必要数量は」「予算は」など幅広い視点から検討します。
②洗い出した前提事項を基に構想設計を行います。
ざっくりした形状イメージを図化し、材質、加工方法、機能性等の当たりをつけます。
機能性と費用面のバランスを考慮して仕様を決めることが大切です。
③構想設計での検討内容に基づき詳細設計を行い図面化します。
必要な形状や寸法を具体化し、公差設定などを詰めていきます。
この時点で具体的な加工方法まで想定し、加工に不利な形状や無理な公差設定を避けることが不要なコストの発生を抑えるポイントです。
また、治具の公差設定に当たってはワーク側、装置側の公差も十分に考慮して、それぞれに矛盾が生じないように注意する必要があります。
④試作し、評価を行います。
試作の重要性
工程導入前に必ず試作品を作成し、設計通りの形状や精度で加工ができているか、機能性や使い勝手はどうか、その他想定外のエラーが生じないか等、設計の妥当性を総合的に確認します。量産、実運用に向けて問題点を洗い出す重要なフェーズです。
必要に応じてN増しでの再評価を行うこともあります。
エッチング加工のメリット:精度とコストの両立を目指す
バリや熱変形を伴わず多穴同時加工を実現するエッチング加工と、エッチング加工で作成した部品を精度良く重ね合わせる積層技術を組み合わせ、複雑で精密な治具を製作します。
レーザーカットやワイヤーカットより加工形状の自由度が高く、切削加工より数量が増えた時のコストメリットが大きく、樹脂成型のような高価なイニシャル費用を必要としない、という非常にバランスの良い加工方法と言えるでしょう。
流路やバネ部品を内蔵するなど、積層構成ならではの構造を容易に持たせられるのもエッチング製治具の特長です。
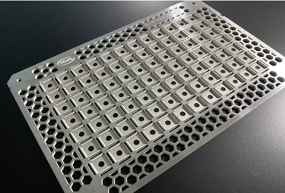
金属エッチング加工+拡散接合による治具
治具設計の外部委託・外注化のメリット
必要となる形状や精度を満たしつつ不要なコストを抑えた治具設計を行うには、それぞれの加工の特色を十分に把握し、最適な使い分けや組み合わせを考慮することが大切です。
治具に求められる仕様を検討するのと平行し、複数種の加工を調査し、最適な加工を選定していく作業は非常に煩雑となるケースが多く見られます。
加工に精通した治具設計のプロフェッショナルに設計を委託することで、自社リソースを治具に求められる要件の整理や他のプロセスの検討に充て、プロセス構築全体の効率化を図ることができるでしょう。
外注業者選定のポイント
外注先の選定の際には製作実績や加工知識に加え、治具の用途や目的、装置側との兼ね合い、プロセス環境等を総合的に考慮した上で製作可能な形状に落とし込んでいく為のヒアリング能力、イメージ力、図面作成力、提案力が十分であるか確認していくことが重要です。
治具設計の事例
エッチング積層治具
切削加工品の図面を元にエッチング加工品に置き換えるのに最適な構成をご提案し、大幅なコストダウンに繋がった。
https://www.toyo-ppm.co.jp/solution/20220417-2/
CCMT採用で基板全体への成膜を実現
横からクランプすることで課題となっていた基板全体への成膜を実現するとともに、一括で固定。
https://www.toyo-ppm.co.jp/solution/20220415-2/
CCMT採用で作業性を改善
「これまでの3倍以上の効率化ができ、導入した検査工程で非常に喜ばれた。」「今後もこの治具を使いたい意向である」と評価をいただけた。
https://www.toyo-ppm.co.jp/solution/20220414-2/
治具の設計や製作はエッチング加工の東洋精密工業にお任せください
製造工程における品質や生産性の向上には最適な治具の導入が欠かせません。
一口に治具製作と言っても求められる要件や加工方法、コストなどを総合的にバランスさせるには幅広い知識と客観的な視点からのアプローチが重要となってきます。
治具製作においてエッチング加工、またはエッチング加工を軸とした複合加工が最適解となる事例は非常に多く、エッチング製治具を設計から製作まで一貫サポート可能な当社のご提案により、大きな改善効果に繋がったとのご評価を数々のユーザー様から頂戴しております。
治具製作をご検討の方、また具体的な治具のイメージまでは至っていなくても工程で何かしらお困りごとをお持ちの方がいらっしゃいましたら是非お気軽にお問い合わせください。
また参考資料も掲載しておりますので、こちらもダウンロードの上、ご一読いただけますと幸いです。