
プロジェクトストーリー
Project Story若手社員が活躍、
試作品の量産効率化と
品質向上プロジェクト
-
回路基板事業部 製造責任者(当時)
1998年入社
田家 義彦 -
回路基板事業部 製造課(当時)
2019年入社
福田 智也
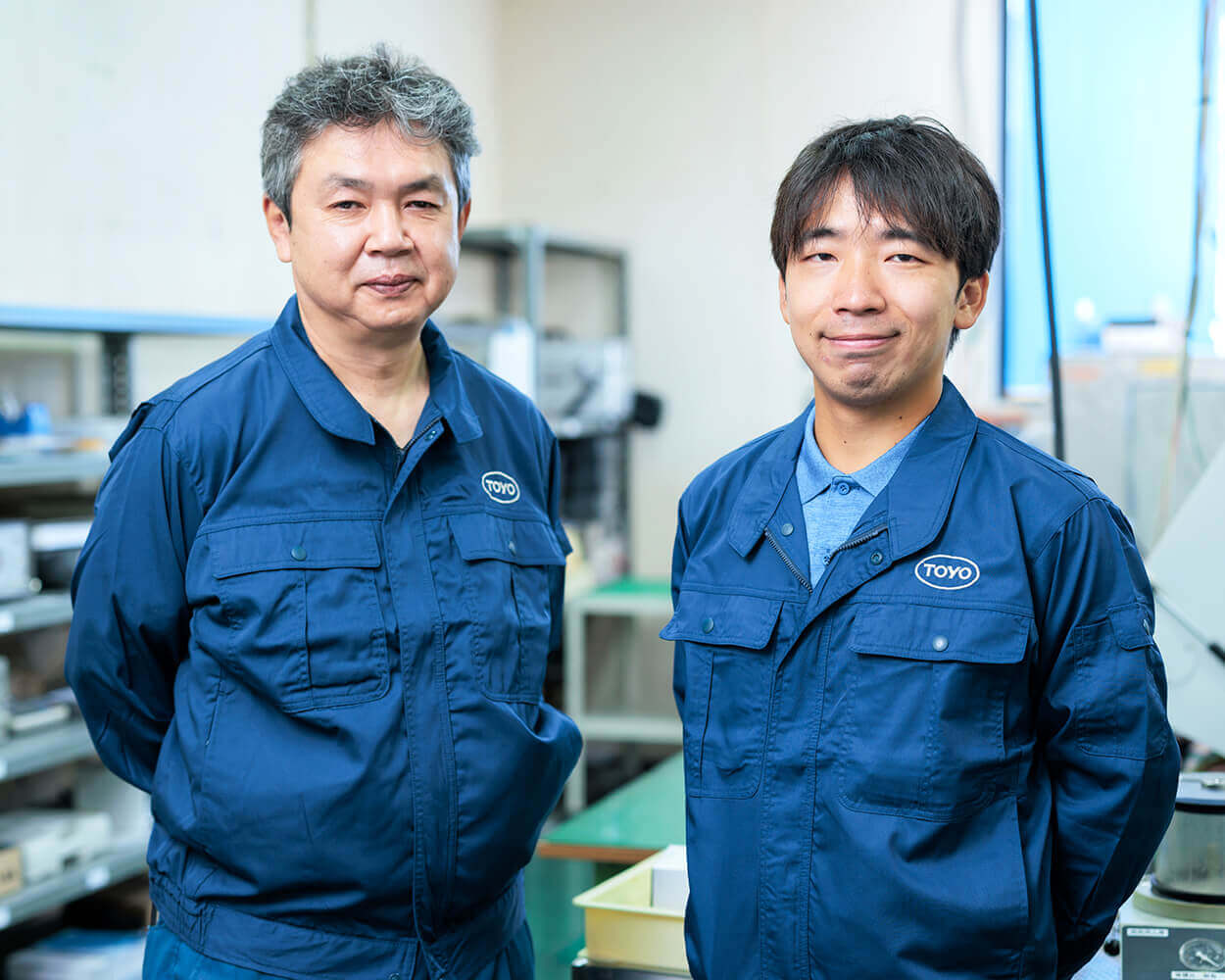
試作品の量産化が決まるも
見えてきた課題
プロジェクトのはじまりは、試作段階であった回路基板の量産化が決まったことだった。依頼元は大手メーカー。これまでに取引がない新規のクライアントだった。フォトリソグラフィ技術を用いて数多くの回路基板を製作してきた当社だが、本案件の回路基板は、社内でもあまり例のない製品だった。
ー“立体形状へのパターン形成品を量産化”
製造部門の責任者田家がこのプロジェクトを担当することになった。
田家「素材的にも形状的にも、これまでのノウハウやプロセスだけにこだわっていては製造できない製品でした。立体形状へのパターン形成自体は何度か試みたことがありましたが、今回はその量産化と品質向上が必須条件でした。」
通常、回路基板はシートや板状の平面にパターンを形成するものが多く、立体形状へのパターン形成品で量産実績はなかった。当時の製造工程では最大でも1日18枚しか作ることができない製品だった。
田家は工程改善に取り組むために4人のメンバーを集めた。その中で、新入社員だった福田を研修も兼ねて参画させた。
処理枚数2.5倍への挑戦
同時に品質の向上も
スタート当時は月産1000枚までの必要性は見えていたため、最低でも1日50枚の製造、つまりこれまでよりも2.5倍の生産量が必要となる。
福田に任されたのは各工程の現状把握と改善だった。
プロジェクトにアサインされてから、福田はこの案件に専属で取り組んだ。
福田は試作段階でネックになっていた工程を担当していたため、その時の知識を活かし、加工テストを通して最適な条件を見定めていった。
周囲のサポートも受けながら徐々にネックになっていた工程の加工条件を整えていった。
問題解決の糸口をつかみ、
事業部としても新たな発見
当時の福田について、田家はこう振り返る。
田家「やろうとしていることのハードルは高いと分かっていましたが、福田が新鮮な発想を持って行動に移していってくれました。そこで発生した問題も一つずつ解決していってくれました。」田家は指導や管理というよりも、福田の持ってきたテスト結果に対してアドバイスをすることに徹した。
田家「フォトリソグラフィという工程は大きく【レジスト塗布】【露光】【現像】という3つに分けられ、今までは作業者が決められた手順で決められた作業を行っていました。しかし、今回は福田がこの3つの作業の加工条件を1つずつ調整してくれたので、工程やメカニズムについても理解を深めてくれたと思いますし、私達にとっても新たな発見がありました。」福田にとって初の量産化プロジェクトは形になり始めていた。
未来創造の主役になろう。